The Ferrari 250 GTO, often hailed as the Holy Grail of automotive excellence, is a legendary sports car that has etched its name into the annals of automotive history. Produced by the Italian marque between 1962 and 1964, this masterpiece was designed to compete in GT racing, and only 39 units were ever manufactured.
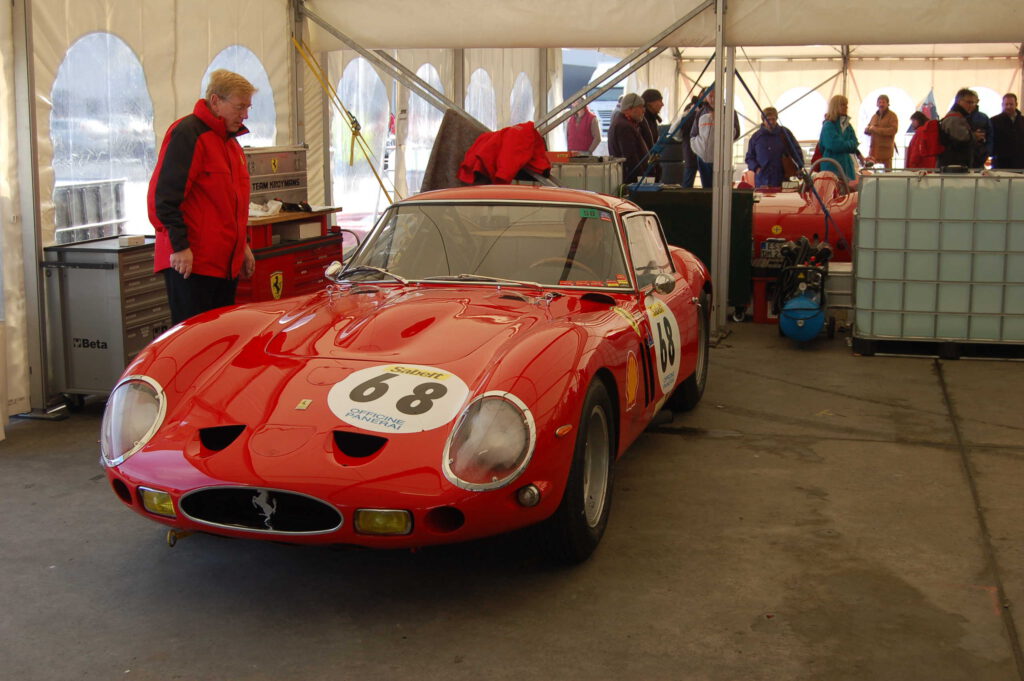
What makes the 250 GTO so iconic is its breathtaking blend of beauty and performance. Its sleek, aerodynamic bodywork was handcrafted with utmost precision, featuring a distinctive long nose, voluptuous curves, and a Kamm-style tail. Under the hood, it housed a 3.0-liter V12 engine delivering approximately 300 horsepower, which propelled the car to a top speed of around 174 mph.
On the racetrack, the 250 GTO proved its mettle by clinching victories in prestigious events like the Tour de France and the 24 Hours of Le Mans. Its success wasn’t just due to its power but also its impeccable handling, thanks to a well-balanced chassis and suspension.
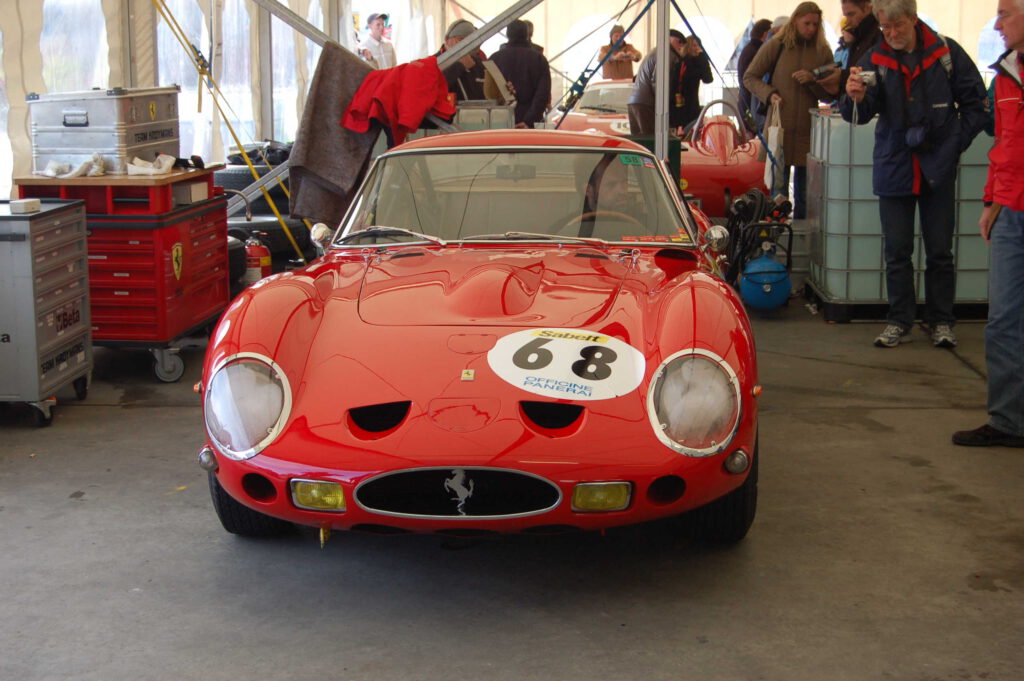
Today, the Ferrari 250 GTO is a rare gem, with collectors and enthusiasts willing to pay astronomical sums to own one. It has become a symbol of automotive artistry, a testament to Ferrari’s enduring commitment to crafting both beautiful and high-performance vehicles.
The body buck model
A body buck, in the realm of automotive design and fabrication, is an indispensable tool that plays a crucial role in the creation of automobile bodies. Essentially, it’s a framework or structure that mimics the shape and dimensions of a vehicle’s body, serving as a three-dimensional reference model during various stages of production.
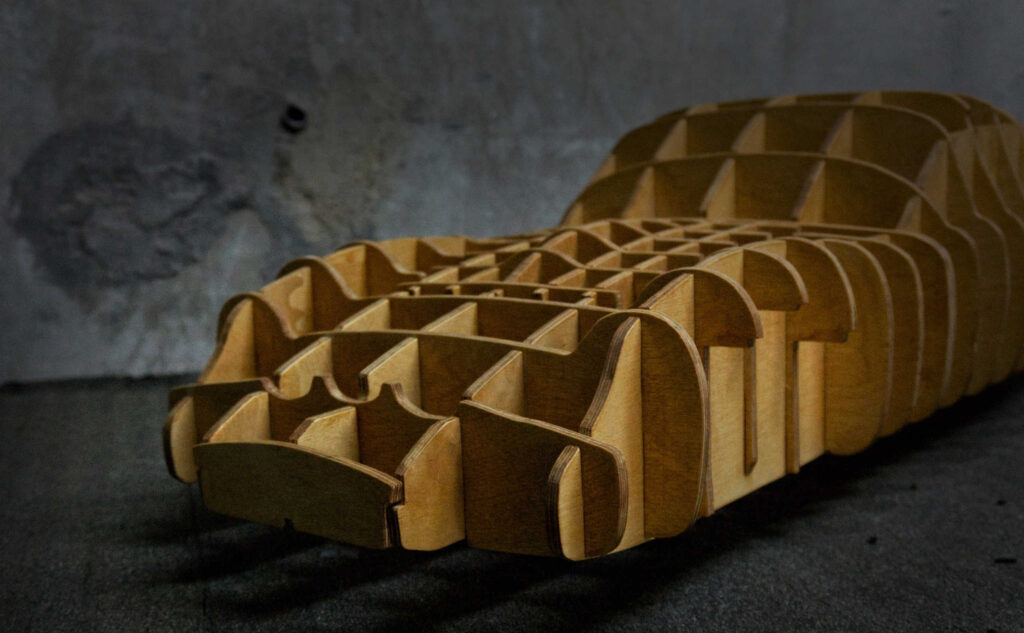
Body bucks come in various forms and materials, but they typically consist of a steel or wooden framework that replicates the precise contours and dimensions of a vehicle’s body. They act as a template for artisans and engineers, helping them shape and assemble body panels with pinpoint accuracy. Skilled craftsmen use body bucks to ensure that every curve, line, and detail of the car’s body matches the intended design.
These tools are not exclusive to automotive manufacturing; they are also used in the restoration of classic cars, custom car building, and even in aerospace and industrial design. The body buck simplifies the fabrication process, ensuring consistency and precision.
In essence, the body buck is the unsung hero behind the scenes, quietly but significantly contributing to the creation of the stunning and aerodynamic forms we associate with our favorite cars. Without it, achieving the perfect bodywork on a vehicle would be a far more challenging and error-prone endeavor.
It took me about 100 hours to complete this unique model. It is 85cm long an weights 6kg.
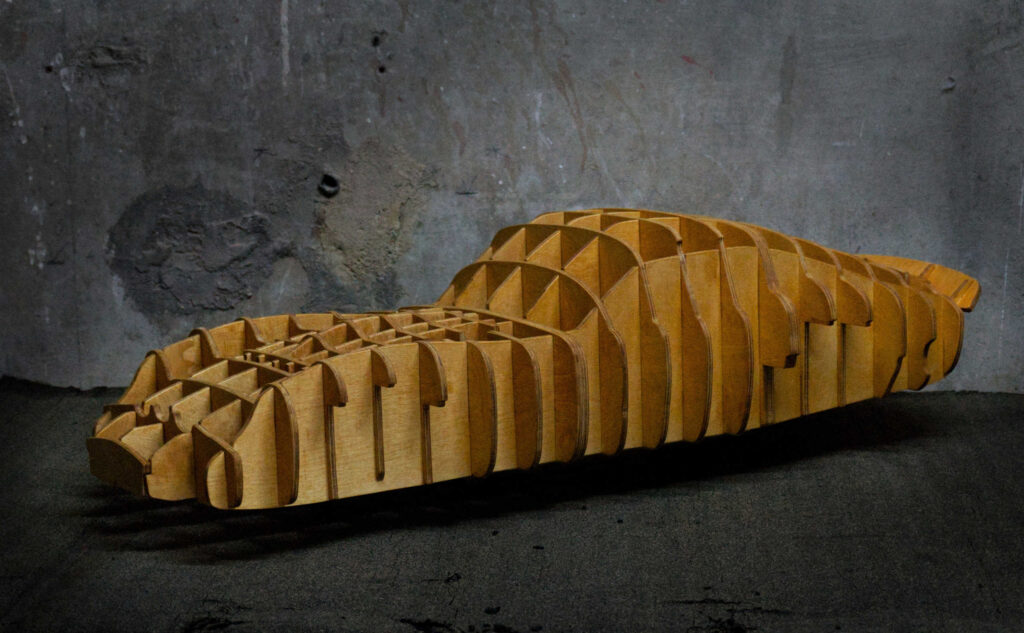
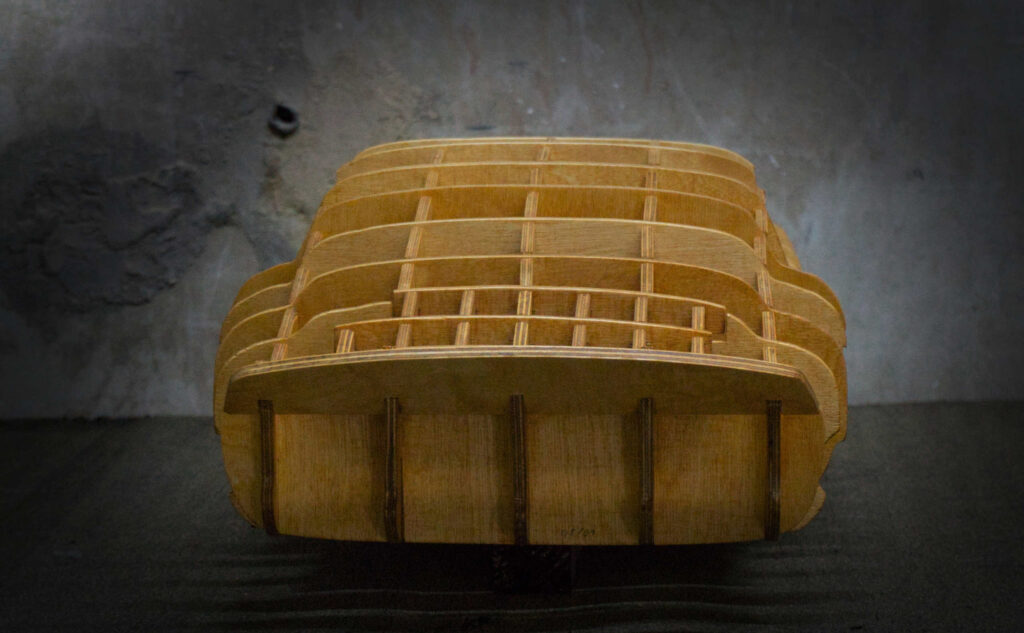
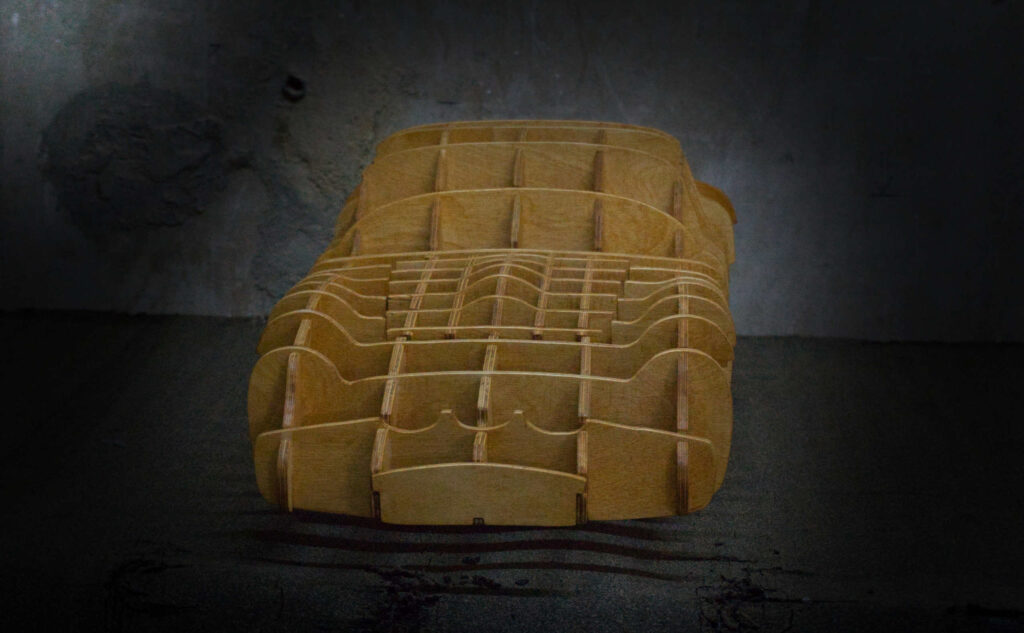